What Is Store Management? 3 Components for Retail Businesses
Overseeing the daily operations of a retail business entails many responsibilities, ranging from training store employees to maintaining the brand's reputation.
By understanding the many aspects of store management and its best practices, retailers can optimize their inventory and enhance customers' shopping experiences. With proper management, retail organizations will be able to maintain efficient control over their business and positively impact their overall productivity.
By understanding the many aspects of store management and its best practices, retailers can optimize their inventory and enhance customers' shopping experiences. With proper management, retail organizations will be able to maintain efficient control over their business and positively impact their overall productivity.
What Is Store Management?
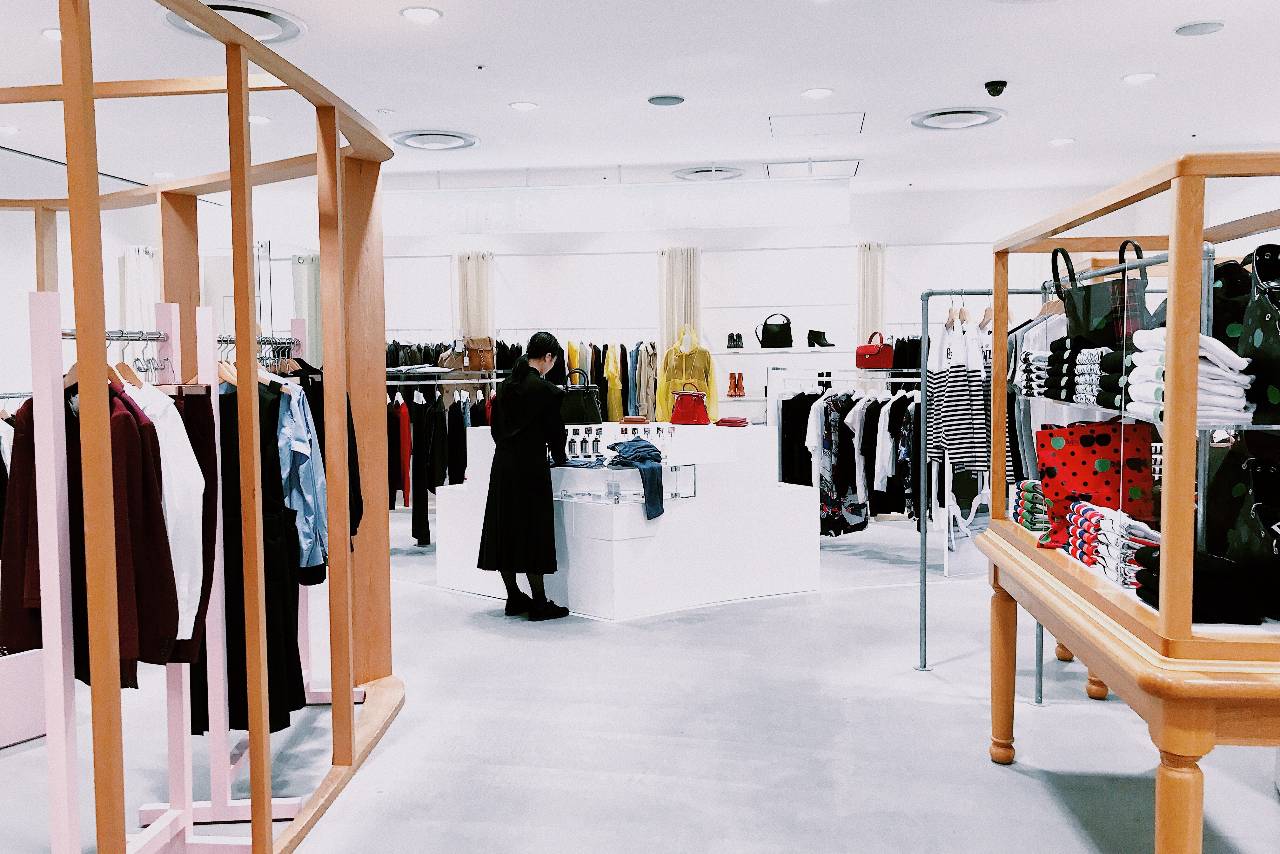
Retail management is the practice of operating and supervising all activities within a store. This includes working closely with staff, creating shift schedules, communicating with suppliers, and dealing with customer complaints.
Store managers have the responsibility of tracking and monitoring inventory levels to prevent stocking too much or too little products. By maintaining the optimal amount of inventory, retailers will be able to meet customers' demands while minimizing unnecessary expenses.
Additionally, they must reach retail sales goals to ensure that the store remains profitable. Store managers also look after their employees' wellbeing and assign tasks to encourage staff to meet their individual sales targets.
In some cases, retail store managers may also assist in strategizing for advertisements on the sales floor and promotions to increase revenue.
Store managers have the responsibility of tracking and monitoring inventory levels to prevent stocking too much or too little products. By maintaining the optimal amount of inventory, retailers will be able to meet customers' demands while minimizing unnecessary expenses.
Additionally, they must reach retail sales goals to ensure that the store remains profitable. Store managers also look after their employees' wellbeing and assign tasks to encourage staff to meet their individual sales targets.
In some cases, retail store managers may also assist in strategizing for advertisements on the sales floor and promotions to increase revenue.
3 Components of Store Management
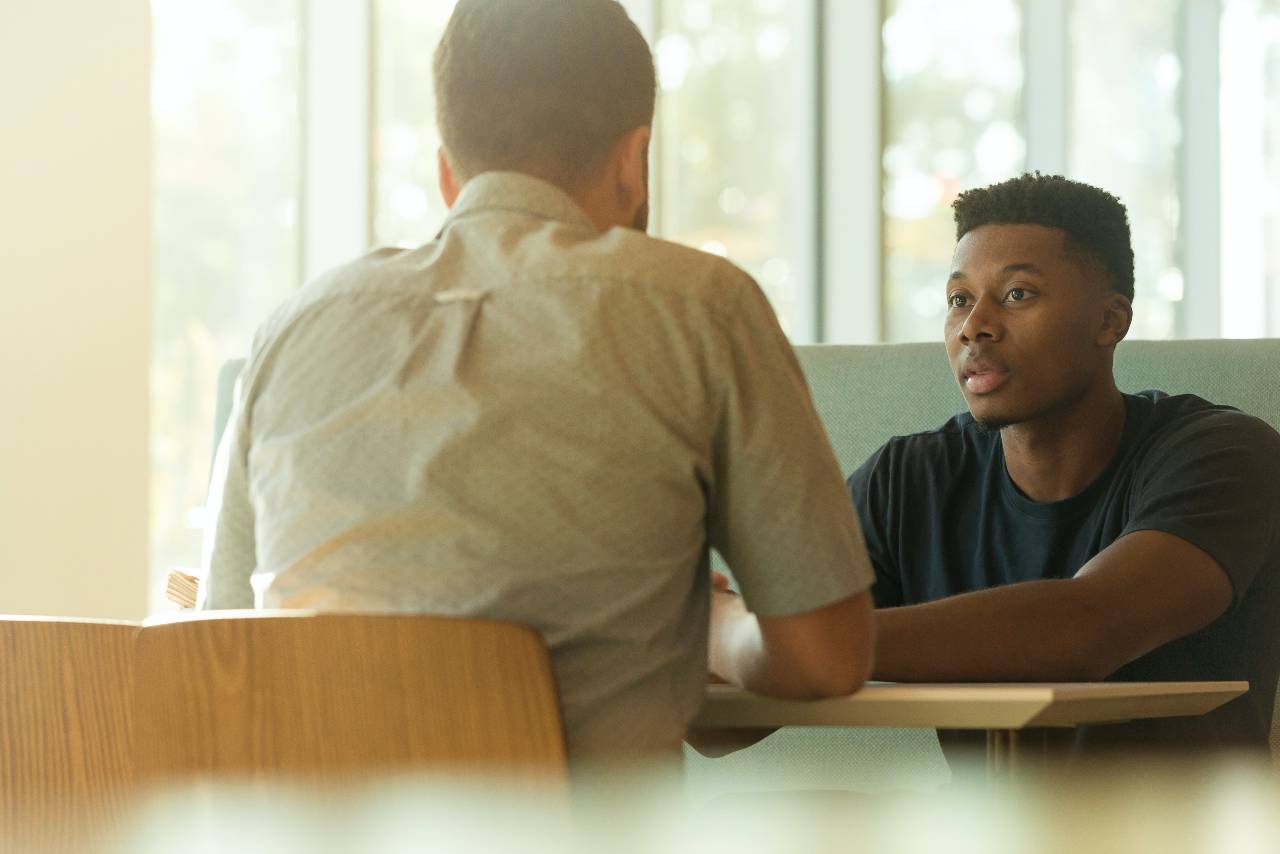
Fulfilling all of the obligations pertaining to the management process can enhance a retail operation's overall success and profitability. The 3 core components of productive store management include-
1. Supporting and Encouraging Staff
According to reports by the National Retail Federation, the retail industry's average turnover rate is above 60 percent. Store managers have an important role in supporting and motivating staff to enhance employee retention. For example, providing incentives or communicating with retail employees can promote a positive environment.
Managers can further reduce employee turnover by effectively administering these employment processes-
During the recruitment process, managers should indicate clear expectations for the role and ask candidates questions that provide insight into how they work under pressure.
To monitor an employee's onboarding progress, managers should set performance goals and milestones for new hires to meet.
Managers can further reduce employee turnover by effectively administering these employment processes-
- Recruiting and Hiring
During the recruitment process, managers should indicate clear expectations for the role and ask candidates questions that provide insight into how they work under pressure.
- Onboarding
To monitor an employee's onboarding progress, managers should set performance goals and milestones for new hires to meet.
- Managing
2. Proactively Controlling Inventory
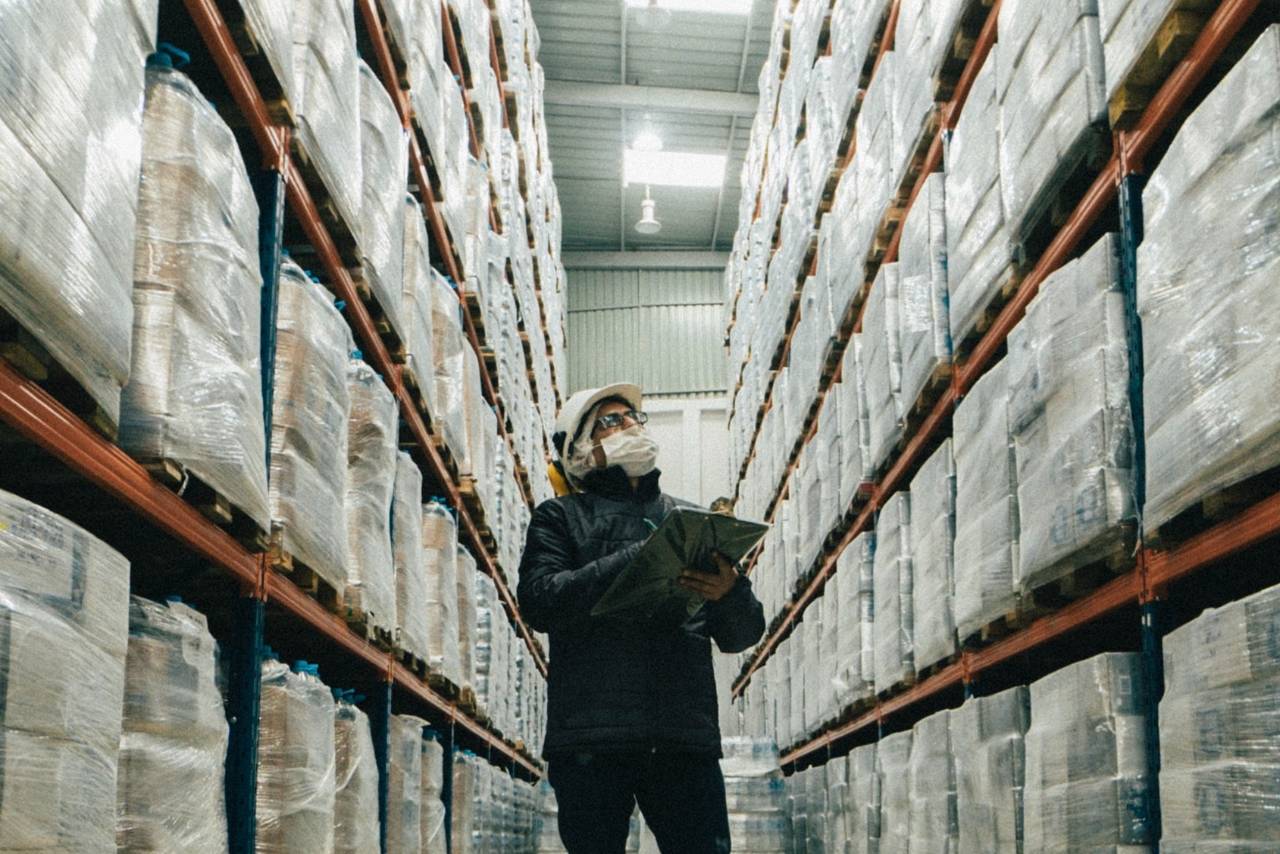
For a retail business to flourish and operate smoothly, inventory must be kept at optimal levels at all times. By properly controlling stock levels, businesses will minimize their risk of profit deficit.
For instance, stock-outs can lead to loss of potential sales and customer loyalty, as shoppers seek competitors to purchase the products they need. On the other hand, overstocking store inventory causes carrying costs to rise since unsold products will take up storage space.
Inventory shrinkage, which is when retailers have fewer items in their actual inventory than what was recorded, is also a concern for store management. Shrinkage is generally caused by theft, product damage, or errors in counting.
To control inventory and mitigate stock-related risks to profits, store management should-
By conducting cycle counts, management can quickly monitor their inventory and identify popular items that may need to be restocked. Also, since managers would be focusing on a subset of inventory, they can finish promptly and spend more time helping customers in their store.
For instance, stock-outs can lead to loss of potential sales and customer loyalty, as shoppers seek competitors to purchase the products they need. On the other hand, overstocking store inventory causes carrying costs to rise since unsold products will take up storage space.
Inventory shrinkage, which is when retailers have fewer items in their actual inventory than what was recorded, is also a concern for store management. Shrinkage is generally caused by theft, product damage, or errors in counting.
To control inventory and mitigate stock-related risks to profits, store management should-
- Conduct Physical Inventory Counts
By conducting cycle counts, management can quickly monitor their inventory and identify popular items that may need to be restocked. Also, since managers would be focusing on a subset of inventory, they can finish promptly and spend more time helping customers in their store.
- Prevent Theft
- Work with Staff
3. Implementing Management Tools
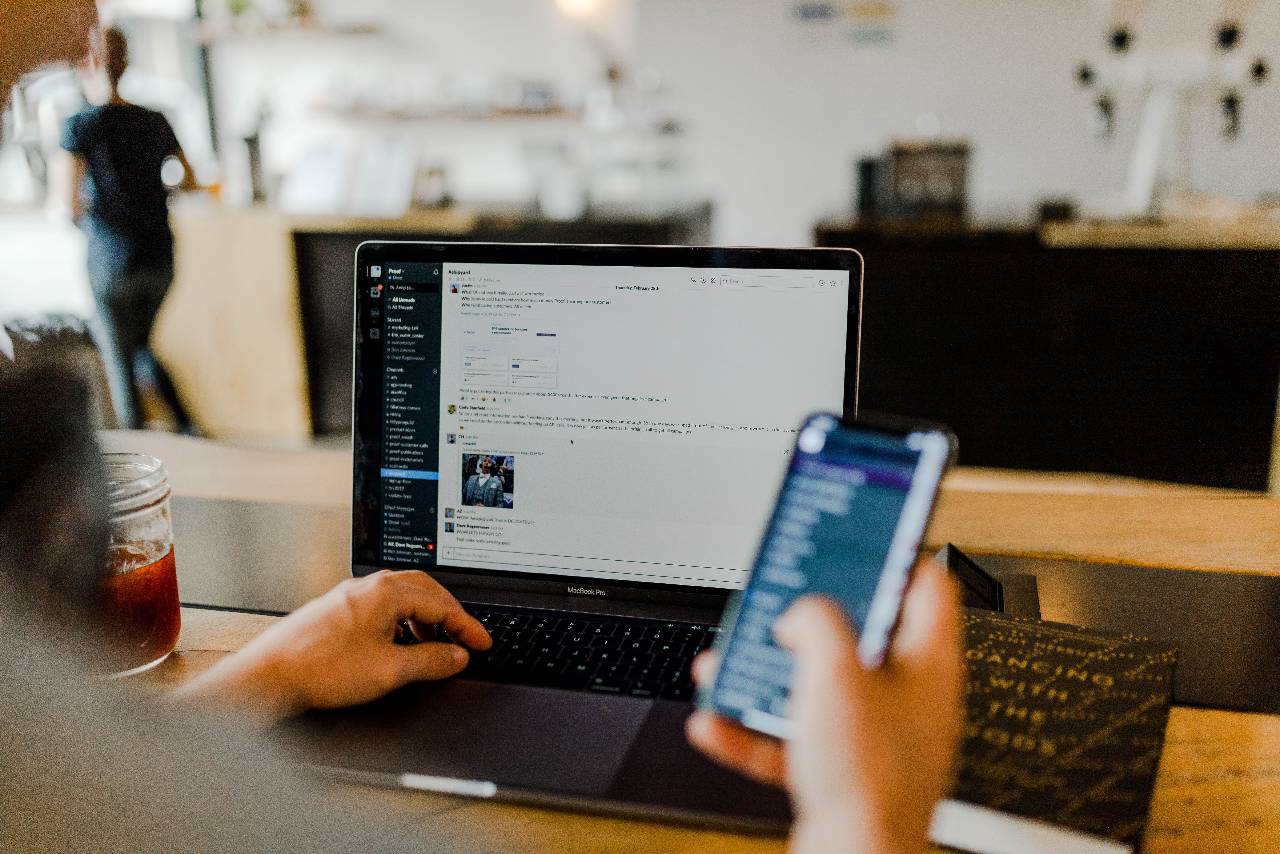
Store management can be streamlined with the latest digital tools and software. For example, retailers can implement cloud POS systems that have advanced features, such as real-time reporting. These solutions can also be integrated with other software, such as inventory management and forecasting. This is important because executive teams will be able to produce data reports, track their inventory, and oversee their financial performance.
Management can take advantage of these tools to maximize their productivity, make data-driven decisions, and promote sales.
Management can take advantage of these tools to maximize their productivity, make data-driven decisions, and promote sales.
Store management comprises a myriad of responsibilities and with effective implementation, retail operations can be productive and customer experience will be enhanced.